Enabling Cargo Traceability Across a Supply Chain
A global provider of logistics services turned to Altoros to create a highly customizable software platform for automating cargo management at each step of the offshore supply chain process.
Summary
Brief results of the collaboration:
- With enabled supply chain visibility, the company helped its customers to save millions of dollars on transportation delays, lost goods, and inefficient vessel loading.
- Streamlining cargo management, the system can be customized to specific logistics and transportation needs in the energy sector—all without coding.
- A microservices-based architecture contributed to the ease of maintenance, while an exposed API further improved supply chain visibility beyond tiers 1 and 2.
- With a white-label solution, the customer got an additional revenue channel beyond logistics, its core business.
- A major Norwegian technology corporation invested in the product and integrated it into a larger digital supply chain suite as a productized offering.
The customer
The company is a global provider of logistics services to the energy industry. Founded more than 50 years ago, the customer operates dozens of supply bases and quays in Norway, Denmark, the United Kingdom, Canada, and Australia.
The need
For years, the customer’s supply chain processes were bogged down by complicated MS Excel- and paper-based workflows. Used by the company for its own operations and contracted shipments, this could often lead to errors, delays, or misdeliveries. As a result, offshore oil and gas rigs or wind plants could lose up to a million dollars per day of idling, waiting for necessary equipment or spare parts.
Lacking engineering talent, the customer turned to Altoros to automate the existing processes and enable cargo traceability in real time. The ultimate goal was to create a highly customizable platform for cargo operators, captains, and lift truck drivers.
The challenges
The team had to address the following issues:
- The customer needed a minimal viable product (MVP) in just 4 months—to reduce human error as soon as possible and showcase the tool to major logistics vendors.
- As cargo containers could have thousands of goods with dynamic sets of characteristics / components and could be involved in diverse processes, including servicing, it was important to ensure high level of customization without coding.
- Despite unreliable Internet at quays and docks, cargo status, weight, and other details such as GPS location still had to be updated.
The solution
Stage 1. After analyzing the requirements, Altoros helped the customer to choose the most important functionality for the MVP, ramping up the team to 10+ Java developers to accelerate the delivery.
Stage 2. The architecture was built upon Microsoft Azure, as the latter had the needed functionality for IoT data ingestion, device management, and compliance. Enabling role-based access in Azure Active Directory—depending on the status and location of a cargo—enforced proper privacy. Using a managed identity service to process personal data helped to conform to GDPR.
Stage 3. Relying on the microservices approach, the team built a customizable Kanban-like board for managing orders, implemented check-lists for inventorying, and visualized the arrangement of containers on a vessel. Placing printed QR codes for goods along with barcode scanners automated cargo tracking at quays. Foot switches enabled to confirm tablet operations when working in gloves.
Stage 4. To address unreliable Internet, the local databases of industrial tablets used by dockers were synced with the server on restoring the connection. After GPS data from the handheld devices was attached to a cargo, the system then visualized approximate location on the map—based on a vessel’s route, delivery time, etc.
Stage 5. To simplify contracting and data sharing, the team implemented an API improving visibility among the participants of the supply chain.
Stage 6. Up to 8 QA engineers reviewed the system before releases, while developers provided further maintenance, integration, and support.
40+
quays served
20+
expert engineers
4
months for an MVP
The outcome
Collaborating with Altoros for over 6 years, the company minimized transportation delays and saved millions of dollars for its customers by automating workflows and enabling product traceability. With a white-label solution that can be customized to industry-specific supply chain needs, the organization got an additional revenue channel. Delivering releases in quick iterations and having an MVP in just 4 months, the customer could continuously adjust it to early user feedback. As a result, a major technology corporation invested in the product and integrated it into a larger digital supply chain suite.
Seeking a solution like this?
Contact us and get a quote within 24 hours
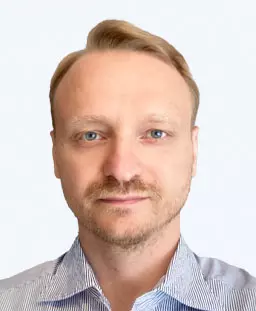