Developing a System for Managing Roof Truss Production
A global provider of smart robotics solutions turned to Altoros to deliver business-critical components for its truss production line.
Summary
Brief results of the collaboration:
- The customer delivered an enterprise-grade solution for managing roof truss production.
- Being part of the first automated truss production line, the system allows for changing the sequence of steps performed by a robot and taking defective elements off the line.
The customer
Operating globally, the company is a leading producer of fully automated solutions for the building component manufacturing industry. With patented smart robotics technology under the hood, the organization provides a revolutionary roof truss production system.
The need
When the customer turned to Altoros, it had an existing CAD-like software—for roof truss designers—implemented as a proof of concept. However, the solution’s functionality was not mature enough to be used in production.
Collaborating with Altoros, the company wanted to optimize the existing functionality, as well as develop some business-critical components.
The challenges
Under the project, the team at Altoros had to address the following issues:
- The system’s immature API with its unpredictable behaviour might cause failures at any step of the truss production line.
- To avoid redesigning defective trusses from scratch, it was important to ensure control of individual truss elements.
- The system’s performance had to be stable even in case of a network error.
- The solution had to be compatible both with the Windows and Linux operating systems.
The solution
Engineers at Altoros delivered two major business-critical components responsible for:
- introducing changes to the sequence of steps performed by a robot at the truss production line
- taking a defective truss element off the production line
To exclude risks of failures, our developers tweaked the system’s API in accordance with the industry standards. Once that was done, the team at Altoros integrated the solution with another proprietary system, which managed truss production itself.
To ensure the system’s stability despite potential network errors, our engineers enabled data buffering and developed a data retransmission mechanism.
With Docker-based virtualization, developers at Altoros ensured the system was agnostic of operating systems in use.
2
components
First
automatic truss production line
€750K
investment raised
The outcome
Partnering with Altoros, the company turned its proof of concept into an enterprise-grade solution capable of customizing the sequence of steps performed by a robot at the truss production line and taking a defective truss element off the production line. With improved API, the system is fault tolerant and minimizes risks of unexpected failures at production.
Seeking a solution like this?
Contact us and get a quote within 24 hours
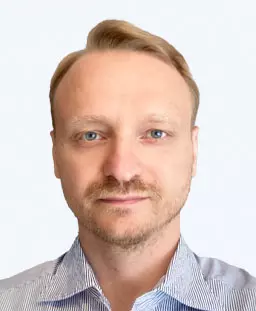